Types and operation of a gearbox
Internal combustion engines are capable of doing a lot today. They generate powerful performance, even at low speeds and with small displacements, while consuming modest amounts of fuel. To harness this potential, a gearbox is essential. If the drive to the rear wheel were transmitted directly from the crankshaft, we would not get very far. Starting could be a problem, not to mention achieving reasonable speeds or driving up hills. To make the engine perform efficiently as a power source, it needs a torque multiplier, which is the gearbox.
- 25 February 2023
- Published by MD
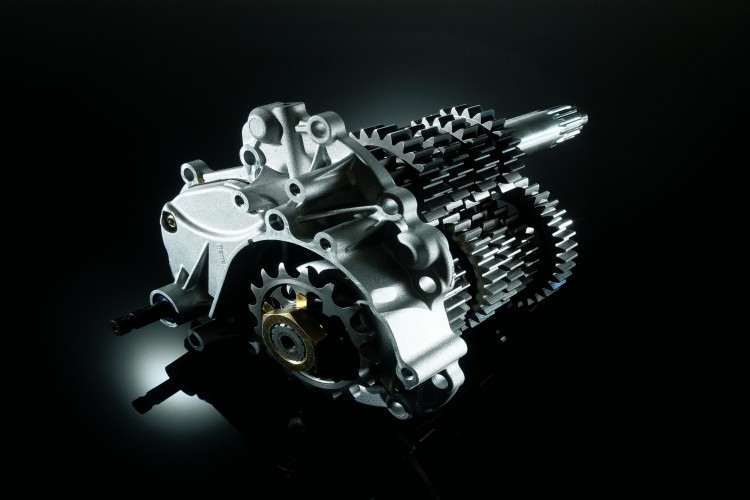
The gearbox can even be called a set of gears in a bicycle, although of course, the constructions used in motorcycles have a completely different, more complex and complicated structure, as the requirements imposed on them are significant.
One-click, a series of movements
The most common type of motorcycle gearbox is a constant mesh manual gearbox, of the sequential type. Sequential, meaning that it allows for the changing of only one gear during one movement of the lever. Such a solution reduces the risk of "stripping" several gears at once, and thus an excessive increase in RPM, which can damage the engine. Selecting only one gear is forced by the design of the control mechanism. When the gear shift lever is moved with the foot, the selector, which is a set of levers, is engaged to move the selector star, in the grooves of which the levers are locked. After such a movement, the gear shift lever returns to its original position.
The movement of the selector star also changes the position of the gear change shaft, commonly called the drum or programmer. The shaft has grooves milled into it, which serve to move the followers. The followers are the elements responsible directly for changing the gear ratio. They move the shifting gears mounted on multi-splines. These gears also serve as a dog clutch, meaning that they have projections on their sides.
The gearbox also contains freely rotating gears on the shaft. All gears are of course constantly meshed together, but the transmission of power to the output shaft and the output pinion only occurs when the dog clutch engages with the cuts in the gear wheels. This principle of operation applies to every manual gearbox, but this does not mean that every gearbox is the same. Depending on the purpose and quality, differences in operating speed and work culture can be colossal.
Precision is essential
Much more depends on gear changes than it may seem at first glance. Quick and smooth execution of this process guarantees not only good acceleration but also the stability of the motorcycle. Each gear change is a momentary interruption in the supply of power, and thus a smaller effect of pulling the chain and gentle compression of the suspension. During tourist rides, this has little significance, but when it comes to racing pace or changing gears in a turn, the impact on handling is significant. Therefore, manufacturers try to make the gearbox components as light as possible and move between them in the shortest possible distance. This is a guarantee of minimizing the interruption in the delivery of driving force to the rear wheel.
Gearbox production is the art of watchmaking. Every aspect of the mechanism's operation depends on the quality and precision of fitting. Another important issue for engineers is to ensure that gears shift smoothly and without resistance. This can be achieved relatively easily by increasing the holes through which the teeth of the shifting shafts enter. However, this cannot be overdone because it is associated with the risk of strong jerks during sudden changes in load, such as rapid accelerations. Generally speaking, creating a good gearbox is an almost watchmaking-like art. How precisely all the gears are fitted together affects every aspect of the mechanism's operation.
One relatively rare way to increase the smoothness of operation is to use bevel gears, which not only work much more quietly and smoothly but also cause much smaller jerks. Unfortunately, such designs are larger, heavier, more expensive to produce, and less resistant to rough treatment. For this reason, smaller and louder mechanisms with simple teeth are more common.
The Battle for Milliseconds
In terms of accelerating gear changes and increasing comfort, the breakthrough turned out to be the use of electronics. We're talking about the quick-shifter, which was initially only available as a sporty novelty, but today is offered in many popular motorcycle segments. Its magic lies in the very short ignition cut-off, causing the revolutions between the shafts to start to equalize and the gear change to occur without the need to disengage the clutch. As a result, the break in power delivery is minimized, the gear change is several times faster, and motorcycle acceleration and handling are much more efficient.
Without a quick-shifter, fast gear changes without the clutch are also possible - with a momentary throttle closure - but drivers don't always manage to do it efficiently enough to smoothly and quickly shift gears without shortening the life of the entire mechanism. The quick-shifter simply brought this process to perfection, and all it took was a simple sensor on the gear shift lever, which detects its movement and sends a signal to the engine control unit to cut off the ignition.
The main element of the quick-shifter is the sensor on the gear lever. The whole system ensures lightning-fast gear changes without using the clutch.
In terms of speed and precision, true masterpieces are the gearboxes in MotoGP motorcycles. They are called Seamless Shift Transmissions, which unfortunately is difficult to translate sensibly into Polish. The exact principle of their operation is unknown to anyone except their designers. It has only been revealed that, in a simplified sense, they work as if two gears were engaged at the same time, and the switch between them lasts a short moment. And a very short one counted not even in tens of milliseconds.
Moreover, in their case, cutting off the ignition or disengaging the clutch is not necessary. Thanks to this, the interruption in powering the rear wheel is imperceptible for the rider and motorcycle. Interestingly, in such a gearbox, it is not possible to select neutral gear via the foot lever. A separate lever on the handlebars is used for this purpose. It aims to eliminate the risk of accidentally engaging neutral gear and at the same time to shorten the shift from first to second gear. And as a result, it facilitates smooth acceleration at the start.
Impressive dual clutches
It is unlikely that the seamless gearbox will find its way into civilian motorcycles, as it is an incredibly expensive and short-lived solution that only works in sports. But that doesn't mean that smooth and instantaneous gear shifting is not for us. Of course, it is! Moreover, smooth gear shifting can take place without our involvement. Although in the majority of motorcycles, the rider is forced to use their left foot to shift gears, in some models, the job can be done for us by an automatic gearbox.
Modern gearboxes are most commonly in the form of a cassette inserted into the engine block, which significantly facilitates their servicing and tuning.
The first serious approach to such a mechanism was made by Yamaha in the FJR 1300 AS model. In this version, gear shifting was semi-automatically operated by servo mechanisms. It is worth noting, however, that it was a classic, manual gearbox, only its control was carried out electronically and was operated via buttons on the handlebars or a conventional foot lever. It was such a big improvement that it did not require the use of a clutch or matching engine speeds. This system, called YCC-S (Yamaha Chip Controlled Shift), did not find followers. Firstly, the quick-shifter turned out to be cheaper, less complicated and faster, and secondly, thanks to Honda's ideas, gearbox automation went in a more futuristic direction.
In 2009, under the banner of the big wing, an innovative, automated, dual-clutch DCT (Dual Clutch Transmission) was shown, whose roots date back to the 70s and the Hondamatic project. Its innovation lies in the use of two sets of clutches mounted coaxially on two shafts, one in the other. This means that changing gears takes only as long as disconnecting one clutch and engaging the other. The duration of such a process is only a few to several milliseconds, which, in the case of a good manual gearbox and a skilled driver, takes about 200 milliseconds.
Today's constructions are very compact and lightweight, while also durable.
The magic of DCT lies in the fact that even and odd gears are operated by separate clutches. This allows for a gear on the currently disengaged clutch to be engaged and ready to transmit power. Of course, not every motorcyclist may appreciate having the work done for them, but it's hard not to appreciate DCT in terms of user comfort and speed of operation. Especially since the computer doesn't have to decide which gear to use - it can be controlled manually through buttons on the handlebars, and nothing stops us from using the traditional foot lever.
DCT gearboxes now have a third generation and have shown great potential for development during this time. The complexity of the design is only slightly greater than with conventional technologies, and the durability of both is at the same level. DCT is only slightly heavier. It's worth noting, however, that it has so far only been used in touring motorcycles, so extreme weight reduction was not a priority for designers.
It's good, but it can be better
Perhaps if the concept of adapting DCT to sports machines emerged, its weight could be significantly reduced. And it must be admitted that a dual-clutch gearbox with its lightning-fast and smooth operation could prove useful here. However, it is currently not used in sports due to FIM regulations stating that motorcycles must have manual gearboxes. But who knows, perhaps someday this will change, and like in cars, dual-clutch gearboxes in sports motorcycles will become standard and allow for more efficient use of engine performance.
DCT gearboxes work much faster and smoother and are not overly complicated.
However, for now, the position of mechanical gearboxes is not threatened, as they are already finely tuned mechanisms. Manufacturers pay great attention to their efficiency, which means that malfunctioning or slow operations are rarely seen today. The precision of execution is an essential aspect here, and advancements in materials and processing techniques can only make things better!